Quality management: Systel recertifies for AS9100
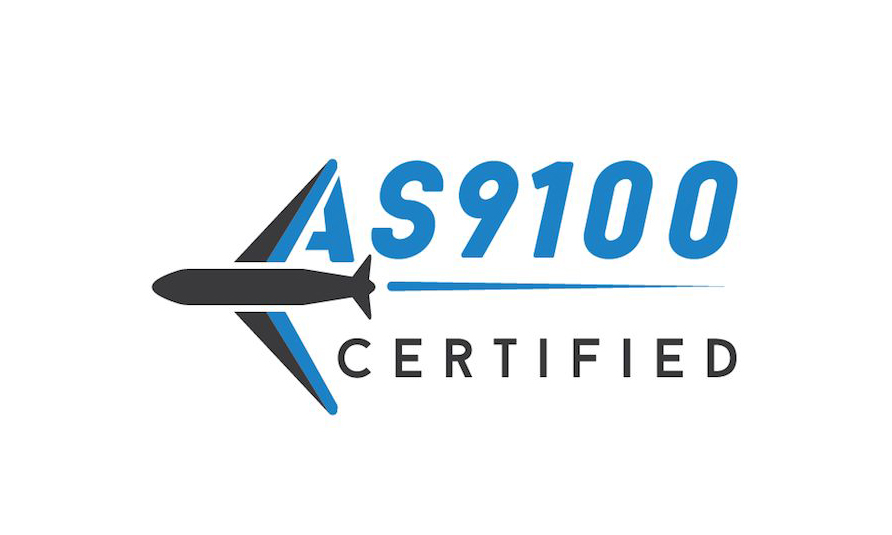
Following industry best practices is crucial to Systel, ensuring that all of our products and processes are compliant with the highest of quality and safety standards. In 2021 we achieved the gold standard in aircraft certification by successfully receiving our AS9100 quality management standard, and are pleased to announce that we have just renewed our certification.
In this blog we will explain what it took for the company to achieve and maintain this standard, and how AS9100 has improved the approach that Systel takes to everything it does.
The AS9100 standard is audited and recertified every three years, with surveillance audits carried out in between. This is the first time that Systel has recertified, and this is a significant achievement for the company.
And this truly is a credit to whole company, not just the quality department. Adoption and implementation must be company-wide in order for this to be successful, and that truly has been the case at Systel.
What exactly are quality management standards?
The standards that oversee quality management ultimately guarantee two things: that products are delivered to customer expectations and that they are delivered on time.
They essentially enforce a standard set of procedures that are well documented and consistently followed, and then in the rare instances that the processes don’t succeed and provide the required outcome, there is a corrective action process embedded.
AS9100 was issued in 1999 by the Society of Automotive Engineers and the European Association of Aerospace Industries and is currently in the ‘D’ iteration that was released in 2016.
It builds on ISO 9001 – a quality management standard that Systel has been certified to for many years – but includes additional requirements specific for aircraft including lot traceability, supplier flow down, electrostatic discharge control, and strict control for foreign object debris (FOD).
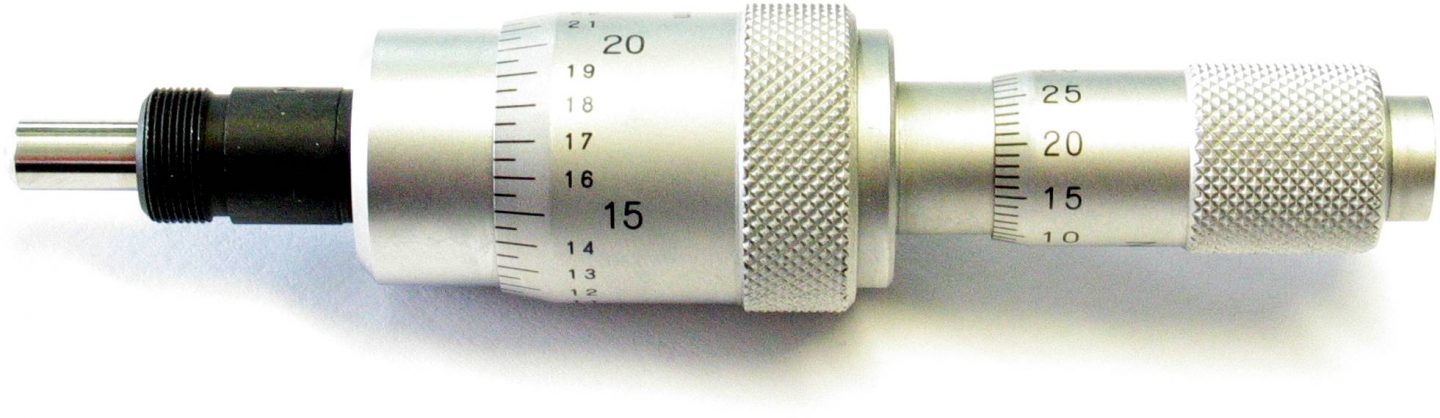
Read More About AS9100 Certification in More Detail Here
What is AS9100?Systel always endeavors to improve its processes to ensure that the highest standards are adhered to, be it US DoD military standards, ISO, or more market-specific requirements such as AS9100.
Why was achieving AS9100 a step-change for Systel?
While it is in our company culture to strive to achieve and maintain many relevant standards, AS9100 was truly a step change in Systel’s approach to quality management, and is something that has improved our processes for the better.
As previously mentioned, AS9100 fully encompasses all of ISO 9001 but with extra safety-critical requirements needed by the aerospace industry.
There are two key details that are important to the successful implementation of a standard such as AS9100:
- The first is leadership buy-in. It can’t be expected that the quality department alone will make everything happen because there are so many processes that other departments not only have to carry out but have to carry out with discipline. Synergy across departments is key, and luckily there is a culture of cross-departmental working at Systel that we could build on for AS9100 implementation.
- The second is ensuring you have a strong internal audit process that will lead to findings where necessary, and then taking actions based on those findings before moving on to the AS9100 registrar audit.
And of course, to do internal audits correctly, you need significant time, and those internal audits need to have internal auditors from various departments. At Systel we’ve worked hard to make sure that we have a good cross-functional team of internal auditors that have been trained and go through in detail with the owners of each of the different processes and audit them and come up with findings. And any internal findings are duly addressed.
Implementing new software tools
One notable area that Systel has improved on is via the implementation of the Arena product lifecycle management tool last year, which has introduced a more digital, procedural, structured and optimized approach to our product development.
Our system level procedures (SLP) that are owned by each department have improved as a result of introducing Arena, as well as to ensure that we meet the criteria for AS9100 compliance.
SLPs are governed by our Quality Manual, which oversees all processes to ensure that they are consistently meeting customer expectations and are delivered on time. This is a key part of ISO compliance, which then also lends itself to AS9100.
Overall the AS9100 process has also improved Systel’s preparation for customer onsite audits and enhanced our supplier flow down process, leading to better quality control. And while AS9100 governs aircraft quality management, implementing it has benefited programs beyond this market as it is becoming a requirement for other areas as well.
Compliance has opened up new opportunities for Systel, enabling us to win and supply into some the biggest programs in the company’s history.
We are proud of what the team has achieved in being recertified to AS9100, and long may adherence to the standard continue.
Initial certification three years ago was a step change in the procedural approach that the business takes to customer requirements, and our recertification is testament to the hard work that continues to be put in by the whole company to ensure that the standard is maintained.
We want to always ensure that we follow industry best practices, and AS9100 is just one way that Systel is showing this. We want to be held accountable and follow the highest possible standards, not only meeting but exceeding expectations, and certifying to these industry standards is just one way that we are meeting this promise.